We spoke to three visionary leaders about how these dynamics are playing out in real time. Their perspectives reveal how companies are adapting to new pressures and priorities, from geopolitics to supply chain resilience. Together, they offer a candid look at the opportunities, trade-offs and real-world strategies behind bringing production closer to home.
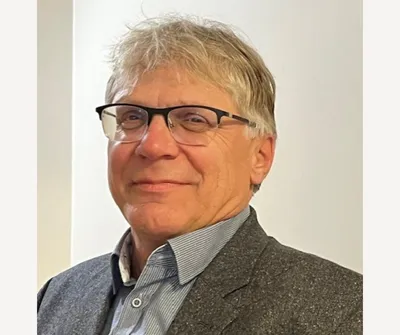
What are the primary drivers behind the adoption of reshoring and nearshoring strategies in supply chain and manufacturing?
Jaro Caban, Global Supply Chain Operations Executive at ProffiZON, Belgium, explains that reshoring and nearshoring strategies can help mitigate long and complex supply chain challenges, such as disruptions, delays and uncertainties impacting supply chain networks and manufacturing footprints. 'The primary drivers behind the adoption of these strategies can be categorised into external and internal factors.
External factors:
- Demand Volatility and Responsiveness - Markets and customer demand are increasingly characterised by rapid fluctuations and volatility, with service expectations often beyond supply chain or manufacturing control. Continuous monitoring and proactive responses are essential to address significant demand shifts.
- Escalating Operational Costs and Trade Barriers - Business costs are escalating due to rising sourcing and customer service expenses, compounded by skilled labour shortages, increased protectionism and new trade tariffs, all adding complexity to global operations.
- Disruptions and ESG Compliance Challenges - Disruptions from economic, climate, health and political factors are causing goods shortages, with ESG compliance impacting international shipping. Logistical congestion, especially in maritime transport, is rising, while pandemic restrictions limit goods movement, causing shipping delays and increased geopolitical risks.
Internal factors:
- Alignment with changes in business strategy requires internal alignment of processes and procedures, leading to strategic shifts in resource allocation within the value chain.
- Transformations and integrations are driven by M&A activities, product portfolio adjustments and alignment with sales strategies.
- The acquisition and implementation of advanced technologies improve control, increase visibility, enable faster or more segmented digital responses, automate processes and create value by reducing unnecessary labour costs.
- Continuous improvement and operational excellence are pursued by addressing inflation, employing lean and agile tactics and learning from competitors' activities.'
The CEO of an Electronics Manufacturing company, Norway, shares his experience regarding the primary driver behind establishing a new factory: 'The need for an alternative to manufacturing in China to serve the North American, European and Asian markets was a key factor. This decision was predominantly influenced by geopolitical considerations, particularly the escalating tensions between China and Taiwan, two of the world’s largest hubs for electronics production. This was the context in 2024. In 2025, however, the post-election and post-inauguration environment in the U.S. has introduced a new array of challenges.
We selected Malaysia for its connections and established electronics infrastructure and its strategic location near Singapore, whose well-developed shipping and offshore industries align with our operations. Furthermore, Malaysia's Western-oriented approach, English-based legislation and well-established electronics manufacturing sector made it an attractive option. However, a complete exit from China was never an option, nor feasible due to the country's vast shipbuilding infrastructure, which would take considerable time for other nations to replicate.'
David Houser, a previous board member at Cybage Software and Infios (formerly Koerber), USA, has led sales and operations and lived abroad, including in China. 'For some time now, many countries have adopted a China+1 strategy. With additional geopolitical issues, tariffs and the understanding that, for example, some raw materials used in the pharmaceutical industry in the US depend on China, this reality has intensified the pressure to make the supply chain more resilient, broader and more challenging to diversify.
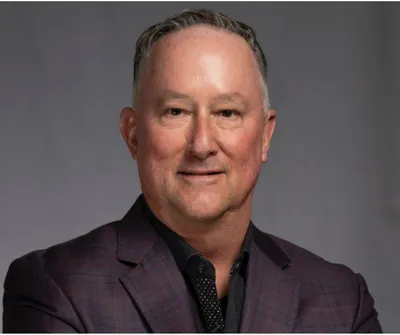
For several years, India has been regarded as an offshore haven for highly skilled, tech-focused individuals at very competitive rates. While this remains the case, new challenges have emerged for India. Global organisations are now exploring other lower-cost options for various needs, particularly for IT and tech-related services. Being in closer proximity to the ‘parent’ time zone, wherever that may be, has become crucial for complex projects. Moreover, India lacks a wide range of supported languages, so nearshoring or reshoring is being considered as a solution to provide in-country language support.
Competition has become more prominent. Consider Costa Rica, parts of Brazil, Colombia, Poland and Eastern Europe. These countries are increasingly favoured by some multinationals for their talent, competitive costs, proximity to key time zones and additional language capabilities. This shift is prompting larger firms in India, for example, to open offices in other parts of the world. While some back-office operations may remain in India, establishing a local office with language support can bridge the gap.'
What key challenges do businesses encounter when implementing reshoring and nearshoring, and what strategies can effectively address them?
Jaro Caban states that in supply chain management, reshoring and nearshoring are two strategies companies employ to optimise their production and sourcing processes. 'These concepts involve relocating business operations from one location to another, aiming to achieve various advantages such as cost reduction, improved efficiency and better control over the supply chain. The following challenges are typically encountered:
- People impacts – When working with third-party vendors and service providers, or relocating your logistics or manufacturing facilities to or within foreign countries, it is likely that you will encounter cultural differences, language barriers and challenges related to cross-cultural collaboration.
- Process impacts – Effective planning and scheduling of supply chain and manufacturing changes require thorough preparation and precise execution. These changes impact quality control of new processes and necessitate vigilant oversight of international contracts, particularly during reshoring. It is crucial to measure performance against targets, swiftly identify deviations, and implement timely corrective actions.
- Technology impacts – These can be significant. Automation, robotics, machine learning and AI are often beneficial for reshoring or nearshoring, supported by existing expertise and user readiness. On the other hand, limited adoption may necessitate a revised strategy focusing on rapid knowledge transfer, education and expert training.
- Performance impacts – Setting appropriate expectations and goals for maturity advancement, as well as for the realisation and adoption of change, is critical to remain business-reasonable and still realise all the planned benefits from the change.
The most effective strategies for addressing these challenges focus on the total cost of change, resilience and sustainability between the current and future states. It's crucial to keep costs and returns within the original business case boundaries. Additionally, the new supply chain and manufacturing infrastructure must fully align with the initial change requirements, resilience and sustainability goals and the end-to-end business framework, including assigned stakeholder resources.'
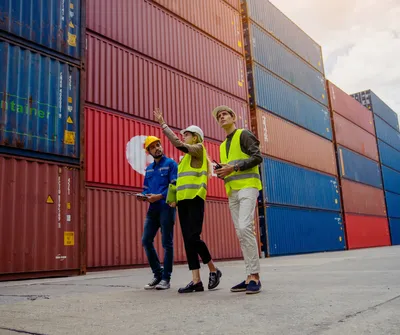
The CEO of an Electronics Manufacturing company points out that the key challenges of reshoring and nearshoring can be divided into two categories: general, global challenges and more specific, local challenges. 'Local challenges differ by country; however, in our case, they included bureaucracy and negotiations with local authorities. A more universal challenge is the securing of the right expertise, which is critical in most locations. To address this, businesses should evaluate the availability of skilled talent as part of their due diligence when considering reshoring or nearshoring. Furthermore, possessing the necessary expertise in the home country is vital for transferring knowledge and bridging local skill gaps. Overcoming these challenges successfully requires allocating sufficient time and resources, as well as ensuring a robust local presence in the initial stages of the transition.'
David Houser emphasises that global organisations need to be competitive in attracting talent that is hard to find, especially when considering the younger generation and their expectations and requirements. 'While work is important, a balance between work and quality of life is equally crucial. For instance, what is the infrastructure like in the area under consideration? Are there sufficient opportunities for recreation, entertainment and family life? What are the costs involved in attracting talent, relocating, or establishing offices to generate interest? How welcoming is the area? What are the tax policies, incentives and other relevant factors?'
How are technological advancements and automation shaping decision-making in reshoring and nearshoring initiatives?
Jaro Caban notes that technological advancement, automation, robotics, machine learning and AI capabilities all help make reshoring and nearshoring not only possible but also cost-competitive in the global marketplace. 'AI, robotics, and automation also make supply chain and manufacturing jobs more rewarding and can transform manual labor into knowledge-based capabilities.
Best practices in automation (e.g., palletization, assembly, sortation, labelling, etc.) are already significantly reducing engineering costs, which in turn lowers total project costs, shortens time to value and improves ROI. Off-the-shelf solutions reduce business risk and lower costs for customers. They can also deliver better margins to system integrators, solution providers of industrial robot systems, advanced automation and industrial Internet of Things (IoT) systems.
Material handling in warehouses and production is another area of automation and robotics innovation that reduces labor costs. Today, palletizers, conveyors, autonomous guided vehicles (AGVs), and autonomous mobile robots (AMRs) already move parts and supplies around factories or warehouse locations in ways that require less labor and operating costs.'
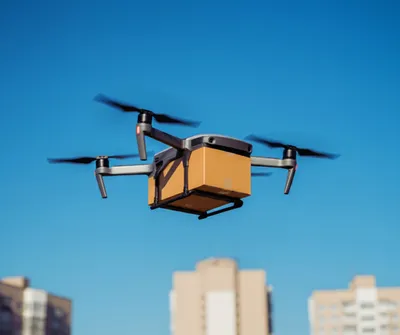
For David Houser, technology is playing a huge part in those decisions. 'In Dubai, for example, a recent forum featured a statement that is truly remarkable: by 2030, the first company to generate $50M per employee will emerge. Looking a few years ahead and considering the disruptive impact of AI on the global workforce, a new lens is introduced for these considerations. Leaders like Dubai become an attractive destination to observe what the future will look like. Countries that fail to keep up will simply be out of touch with attracting reshoring and nearshoring opportunities. I will leave the audience with this to reflect upon. As I have mentioned on numerous podcasts and projects, the future will be defined as follows:
A - automation, autonomy and AI;
B - larger data sets, with the advancement of quantum computing to address complex questions by 2030;
C - Everything will be on the cloud; those not on the cloud will fall behind;
D - Finally, all devices will operate in harmony.
If we consider the ABCs now, they are vastly different from those we learned in school. Just focusing on my “A”: How will we, as humans, manage this scenario? Vehicles will become autonomous, working with advanced AI algorithms for fast decision-making. Accident rates will drop, insurance costs will decrease and goods delivery will become more efficient. While this all sounds promising, what about the loss of jobs and the potential rise in global unemployment? This will create unprecedented change. Stay tuned, as the next 5-10 years will bring fascinating transformations.'
Summary
As industries adapt to changing economic, geopolitical and technological landscapes, the importance of staying flexible and responsive will continue to grow. While challenges remain, these strategies offer opportunities to strengthen local economies, enhance supply chain control and embrace new technological advancements. The future of global manufacturing will be shaped by how companies navigate these changes, making it essential for businesses to remain forward-thinking and prepared for the evolving landscape ahead.
The Kestria Industrial/Production Practice Group excels in sourcing leaders who navigate the complexities of modern industries. With expertise in sectors like manufacturing, energy and automotive, Kestria helps organisations find transformative leaders who drive operational excellence, foster innovation and guide companies through technological disruption. Committed to shaping the future of industrial production, the group delivers leadership for an evolving landscape.